RFID-Technologie:
Flexible Produktion und hohe Variantenvielfalt
Trotz zurückliegender Finanz- und Wirtschaftskrise verzeichnet die Radiofre- quenzidentifikations-Technologie (RFID) derzeit ein Volumenwachstum von mehr als 20 Prozent und ein Umsatzwachstum von 10 Prozent pro Jahr. Aktuelle Trends und Marktzahlen führender Institute wie ABI oder IDTechEx präsentierte Klemens Sattlegger von Texas Instruments Deutschland auf der Transponder-Roadshow, einem losen Zusammenschluss von Herstellern und Systemintegratoren rund um das Thema RFID. „Deutschland stellt derzeit vor Großbritannien und Japan den drittgrößten Markt weltweit für die Radiofre- quenzidentifikation mit Ausgaben von über 400 Millionen US-Dollar pro Jahr“, berichtet Sattlegger. An der Spitze des Rankings liegen die USA noch knapp vor China mit einem Volumen von jeweils über 1,4 Milliarden US-Dollar.
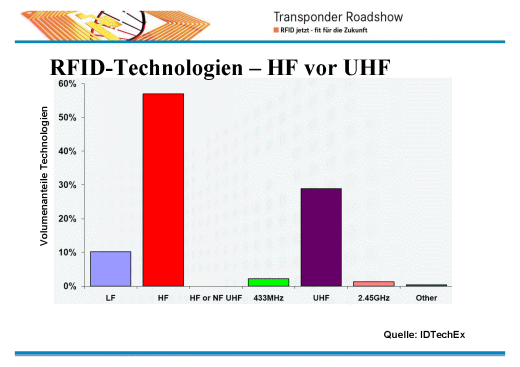
Bei den verschiedenen gängigen Technologien haben Transponder im Hochfrequenzbereich 13,56 MHz volumenmäßig derzeit am Markt klar die Nase vorn, gefolgt von der Ultrahochfrequenz-Technologie, die zwischen 868 und 915 MHz Daten sendet und empfängt. Auch bei der Wertschöpfung bzw. Umsatz liegt die HF-Technologie vorne, jedoch vor LF 125 -134kHz und aktiven Transpondern. Die UHF passiv Technologie liegt hier an vierter Stelle.
Weitere Trends und Innovationen sieht der Texas Instruments-Experte in neuen Transpondertypen, die auch deaktiviert werden können, oder den mittlerweile verfügbaren aktiven Transpondern mit eingebautem Sensor und Interface. Sattlegger: „Diese etwas teureren Typen können beispielsweise in Behältern den Druck messen oder eignen sich für die Containerortung in Echtzeit.“ Interessant seien auch neue Finanzierungskonzepte der Systemintegratoren, beispielsweise über das Leasing-Modell.
RFID-Einsatz in Industrie und Produktion
Verschiedene umgesetzte RFID-Projekte in Industrie und Produktion, insbesondere in der Automotivbranche, stellte Dipl.-Ing. Herbert Hohmann, Prokurist Sales Automotive, von der deutschen Landesgesellschaft des in Österreich beheimateten Unternehmens Identec Solutions vor. In der Endmontage bei Audi in Neckarsulm werden täglich 800 Fahrzeuge gefertigt. Typische Kennzeichen für die Automobilproduktion im Premiumsegment sind heute eine kundenspezifische Endmontage und dezentrale Automatisierungsarchitektur: Das Fahrzeug selbst bringt auf einem Transponder Daten für seine eigene Fertigung mit. „In den einzelnen Bearbeitungsstationen liest die Betriebsmittelsteuerung die Daten aus und fährt ihre eigenen Programme“, verdeutlicht der RFID-Spezialist. Von daher sei in Neckarsulm die Endmontage eine Fortsetzung der gleichen Transpondertechnologie, die schon in den Schweiß- und Lackieranlagen genutzt wird.
Die meisten der überwiegend aktiven Transponder arbeiten beim Automobilproduzenten auf der Frequenz 2,45 Gigahertz. „Damit wird sichergestellt, dass nur der Chip gelesen wird, der wirklich in der Fertigungsstation steht und nicht davor oder dahinter“, so der Identec Solutions-Experte. Während des gesamten Fertigungsprozesses werden auf die Tags ständig weitere Qualitätsdaten geschrieben, die dafür sorgen, dass das Fahrzeug ggf. in der Endmontage noch einmal nachbearbeitet werden kann. Hohmann: „Insgesamt sind bei Audi in Neckarsulm rund 1700 Transponder im Einsatz.“
Individuelle Wirtschaftlichkeitsrechnung
Im Unterschied zu dem vorgestellten Projekt Neckarsulm, wo aktive, wiederverwendbare Transponder eingesetzt werden, setzt der schwedisch-chinesische Automobilkonzern Volvo im Werk Gent in einem ähnlichen Projekt auf passive Tags im 865-MHz-Bereich. Hohmann: „Diese sind natürlich um ein Vielfaches günstiger, können aber nur einmal verwendet und müssen am Ende des Prozesses entsorgt werden.“ Für welche RFID-Technologie man sich letztendlich entscheide, müsse eine individuelle Wirtschaftlichkeitsrechnung ergeben.
Aber auch andere Industrien können mit Hilfe der RFID-Technologie ihre Prozessabläufe optimieren: So hat sich beispielsweise der Badewannenproduzent Bette GmbH in Delbrück dafür entschieden, keine Massenware mehr herzustellen, sondern auf ‚Made to Order‘ zu setzen. Badebegeisterte können heute unter 500 Modellen in 30 Farben wählen, die dann individuell produziert werden.
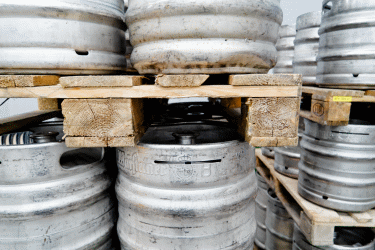
|
Foto: Dematic
|
Bierfässer mit Schlitz und Transponder.
Bei dieser Produktionsumstellung entstand der Bedarf, einzelne Chargen und Wannen auch zu identifizieren. Die Lösung des Problems für Bette war ein 13-MHz-Chip, der in Scheckkartenform mittels Magnet an den Wannen befestigt wird. Hohmann: „Dort sind alle Produktionsabläufe und Muster hinterlegt.“ Die Betriebssteuerung könne auf Basis dieser Daten durch Scannen erkennen, wohin die Wanne für den nächsten Fertigungsschritt gesteuert werden muss.
„Der Markt treibt die Unternehmen dahin, ihre Produkte individuell und in hoher Variantenzahl bei gleichzeitig abnehmenden Losgrößen anzubieten“, zieht Hohmann ein Fazit aus diversen durchgeführten industriellen RFID-Projekten. Als Voraussetzung für die heute in der Produktion geforderte Variantenvielfalt inkl. individuell identifizierbarer Produkte hätten viele Firmen bereits eine flexible Produktionsstruktur mit einer entsprechenden Logistik dahinter aufgebaut. Hohmann: „Als letztes Glied bedingen diese veränderten Produktions- und Prozessabläufe auch in den Betriebsmitteln eine entsprechende Mobilität, die die Logistik wirkungsvoll unterstützen kann.“
Veröffentlicht in: „Produktion“ und „Deutsche Logistik-Zeitung (DVZ)“
© Harald Lutz 2010 
|